Hoe ontwikkel je binnen een jaar een helm die tegen alle vormen van geweld en krachten bestand is? Het was de vraag waar alle fabrikanten in 2018 van wakker lagen. Schuberth loste het raadsel als een van de eerste op en haalde zo Max Verstappen binnen. FORMULE 1 ging op bezoek in de fabriek en kreeg uitgelegd hoe het bedrijf dat voor elkaar kreeg.
De ontwikkeling en productie van Schuberth-helmen is voor het grootste deel in handen van het Italiaanse bedrijf Teca25, opgericht in 2004 en sinds 2014 onderdeel van de Duitse helmfabrikant. Het opereert vanuit Schio in Noord-Italië en heeft een ontwikkelingscentrum in Bassana del Grappa, een uurtje rijden van het hoofdkantoor. Hoewel je bij een gevestigde naam als Schuberth zou verwachten dat de helmen in een enorme fabriek aan de lopende band worden gemaakt is het tegendeel waar. In de workshop zijn acht mensen werkzaam en zij maken de helmen van onder meer Daniil Kvyat, Carlos Sainz en Max Verstappen met de hand.
Een combinatie van wetenschap, ambacht en kunst. Het is zo’n nauwgezet proces vol geheime technieken dat Teca25-oprichter Alberto Dall’Oglio aan het begin van de rondleiding nog wat onwennig vertelt over de werkzaamheden. Niet eerder opende het bedrijf de deuren voor de media. “Wij laten foto’s maken, maar ik zal nog wel even checken wat we naar jullie opsturen”, zegt hij lachend maar toch gemeend. De weg die hij met zijn bedrijf heeft bewandeld naar de ontwikkeling van de SF3, de helm die voldoet aan de nieuwste eisen van de FIA, was namelijk een lange.
Lees ook: Vlag ging uit bij helmfabrikant Schuberth toen Max Verstappen tekende
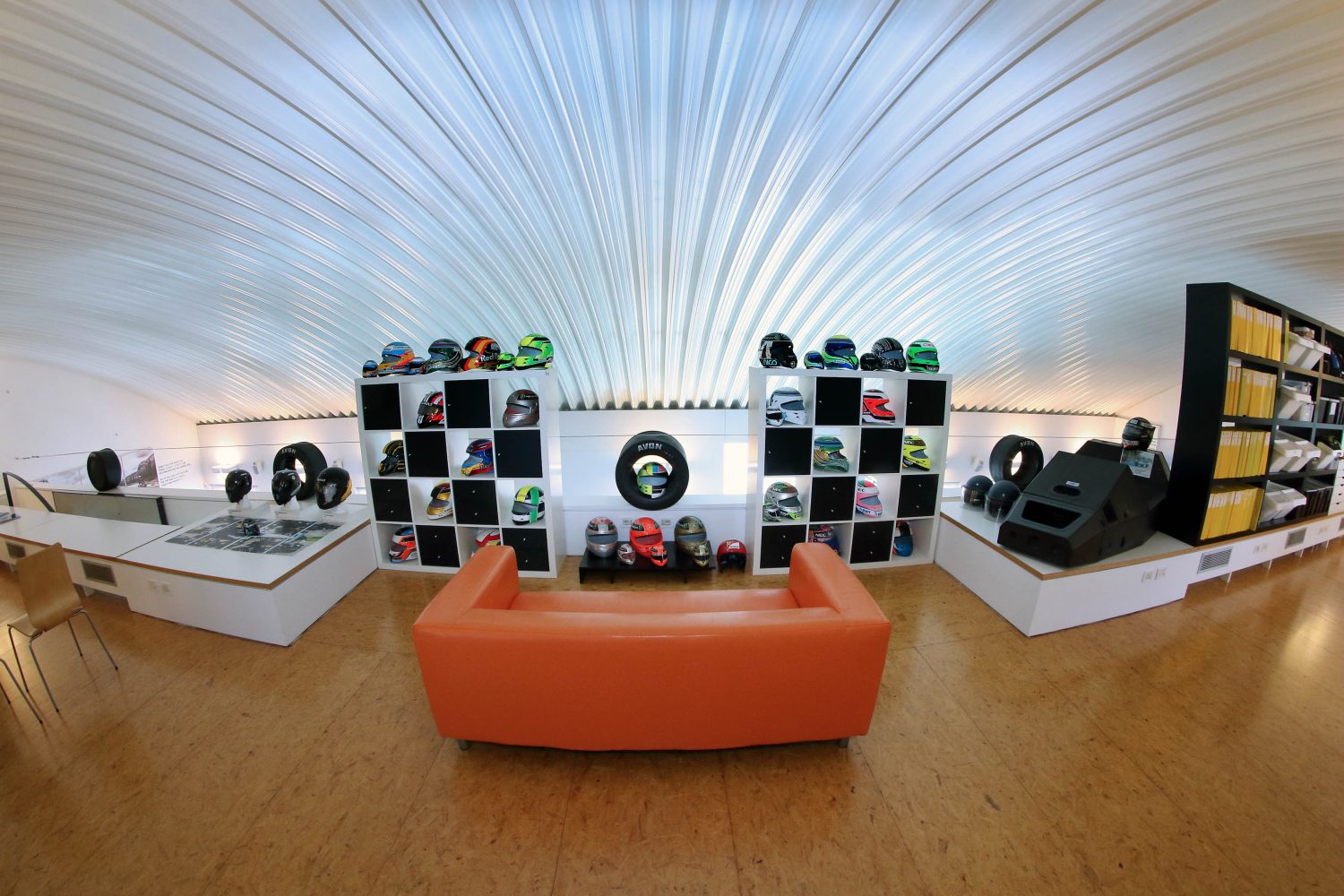
Foto: Schuberth
De aanleiding
Het begint in 2009 met het ongeluk van Felipe Massa. De Braziliaan wordt tijdens de kwalificatie voor de Grand Prix van Hongarije vol op zijn helm geraakt door een losgeraakte veer van een andere auto. Massa komt met een schedelbreuk goed weg en overleeft het ongeluk. Dat de veer dwars door het vizier is gevlogen, zet de FIA aan het denken. In eerste instantie komt er een eisenpakket volgens de standaard 8860-2010 en krijgen de vizieren een strip aan de bovenkant. Die is gemaakt van zylon, materiaal dat ook wordt gebruikt bij kogelwerende vesten. “De strip was niet de beste oplossing, maar wel de beste op dat moment”, vertelt Dall’Oglio. “Hij moest er na de productie van de helm steeds met de hand op gemonteerd worden.”
Het nieuwe helmreglement 8860-2018 van eind 2017 biedt fabrikanten tot 31 december 2018 de tijd om de strengere testen te doorstaan. Het maakt de helmen 12 tot 22 procent veiliger, rekent de FIA voor. “Eén ding is zeker: als Felipe Massa de nieuwe helm zou hebben gedragen in 2009, was er niets aan de hand geweest”, beweert hij. Maar de eisen van de FIA dwingen hem en zijn bedrijf in een spagaat of, zoals hij het zelf zegt: “Je wilt je vrouw dronken voeren zonder dat de fles leeg raakt.”
Lees ook: Longread: Vettel, Schumacher en Verstappen, iedereen in de kleuren van helmkoning Jens Munser
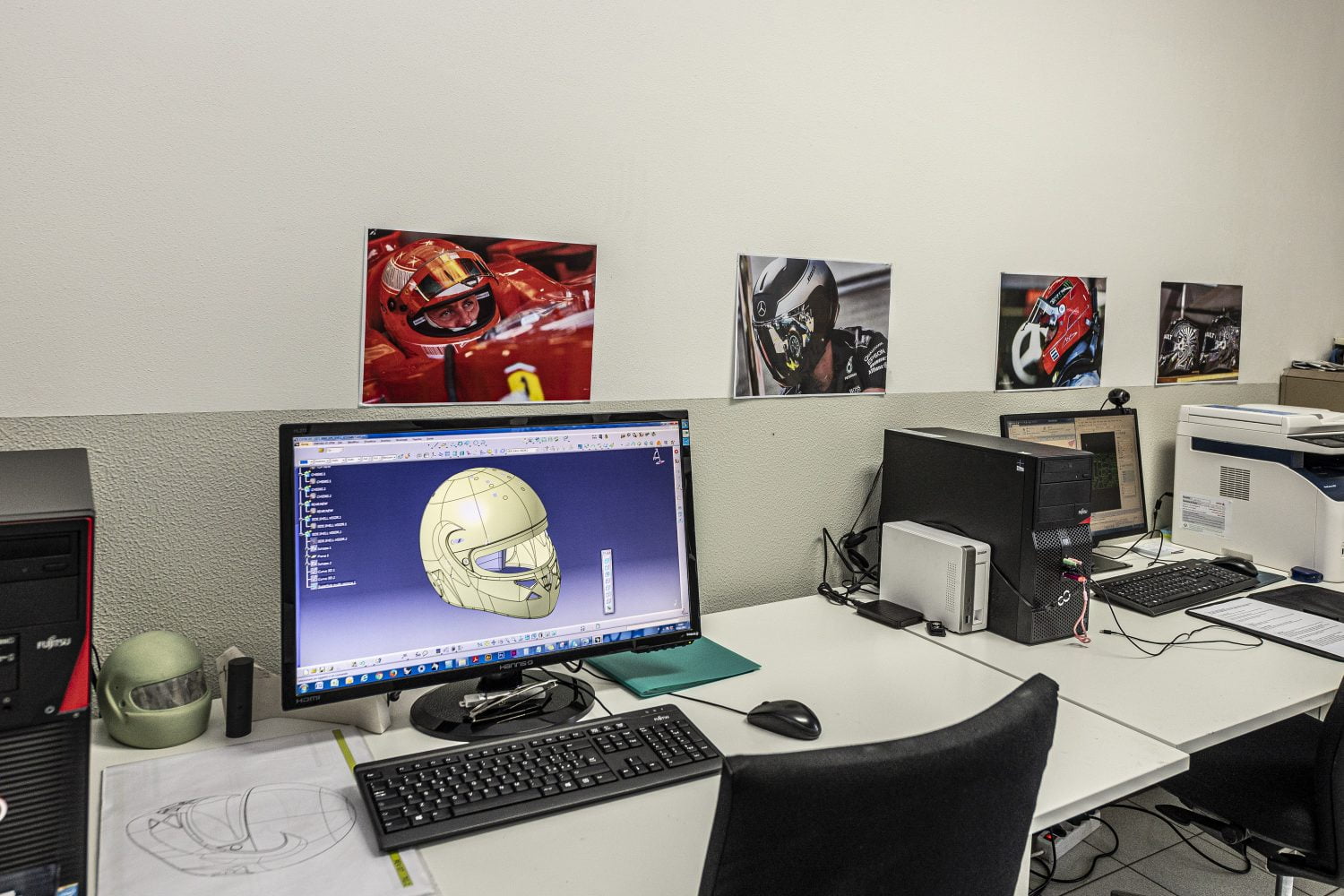
Foto: Schuberth
De kopzorg
Daarmee doelt Dall’Oglio op de tegenstrijdige crashtests voor de helmen. De schelp, het koolstofvezel omhulsel van de helm, moet namelijk zowel hard als flexibel zijn. “Dit heeft de FIA echt onderschat. Achter de cijfers leek geen research te zitten, alsof ze uit de lucht waren gegrepen. De opdracht was om een helm te ontwikkelen die ballistische tests doorstaat, waarbij een projectiel van 225 gram tegen de helm wordt geschoten. Maar een impact van 20 kilometer moet hij ook kunnen weerstaan. Dat is verschrikkelijk ingewikkeld, het zijn twee totaal verschillende vormen van bescherming. Voor impact bij lage snelheid heb je zachtheid nodig, voor hoge snelheid juist stijfheid. Totaal het tegenovergestelde dus en om dat combineren was het probleem.”
Om er vervolgens nog maar een metafoor tegenaan te gooien: “Het is als een korte deken: kies je voor koude benen of koude armen?” Bovendien wordt het testgebied van de helm met een centimeter uitgebreid en moet de maximale belasting op het hoofd van de coureur bij een directe impact omlaag van 300 naar 275 G. “Voor de impacttests zou je een metalen helm kunnen maken, maar die brengt in zo’n situatie alle energie over op het hoofd. Die klap overleef je niet.”
Hulp van buitenaf kan Dall’Oglio niet inroepen, literatuur is er niet. “Het was echt vallen en opstaan,
trial and error. Als je na een gefaalde test iets aanpaste, faalde je voor een andere. Ik dacht vaak licht aan het eind van de tunnel te zien. Dan laadde je de bus vol helmen en reed je vol vertrouwen naar het FIA-laboratorium, hopend dat je terug zou keren met de homologatie. Maar nee, dan reed je met de tranen in je ogen terug.”
Lees ook: Gasly rijdt eerste GP van 2020 met speciale door fan ontworpen helm
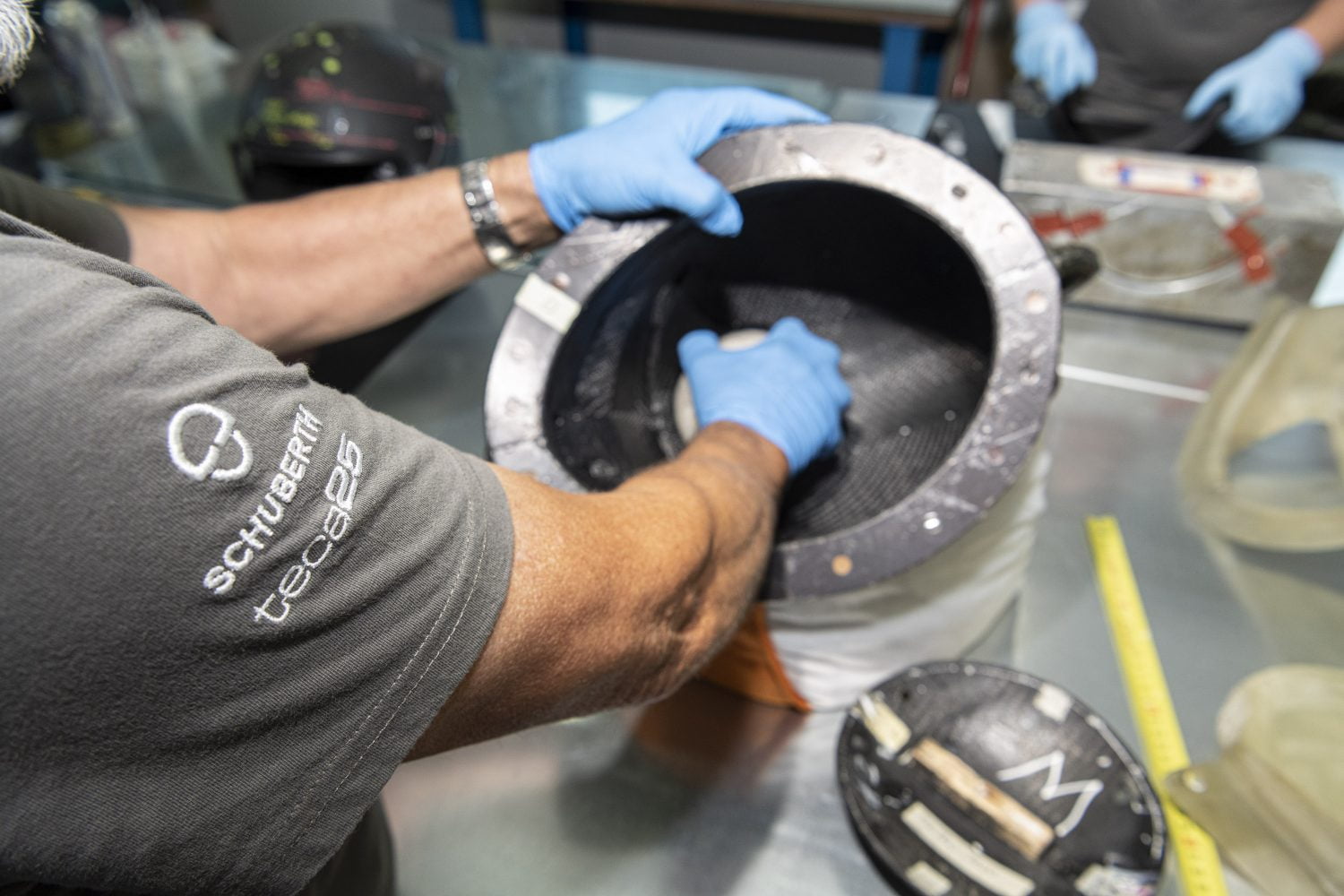
Foto: Schuberth
Het examen
De eerste versie wordt begin 2018 getest, sindsdien zijn er vele schelpen gesneuveld. Voor elke test zijn er negen nodig met tien manuren werk erin en een waarde van zo’n 7.000 euro. Dall’Oglio schat het gebruikte aantal op 150 exemplaren. Het zorgt voor enorme stress in helmenland: wie is op tijd klaar voor de wintertest in Barcelona? “Zeker, het moest veiliger, maar het was erg lastig te realiseren in één jaar. Concurrenten, merken die we enorm respecteren, konden het niet op tijd afkrijgen. En dat begrijp ik volkomen, het was ongelooflijk moeilijk. Stilo was uiteindelijk de eerste, wij de tweede. Bell en Arai hadden het zwaar. Wij slaagden op 23 december, net voor de deadline dus.”
Trots laat Dall’Oglio een filmpje zien op zijn telefoon. Het is de allerlaatste test waarbij met grof geweld aan de helm wordt getrokken. “Een test van het Hans-systeem (head and neck support, red.), waarbij het hoofd niet mag bewegen. De helm moet de kracht opvangen, want als er speling zit op het hoofd breek je je nek. Let op mijn gezicht, haha! Zelden voelde ik zo’n druk als op dat moment. Hier besef ik dat we het gehaald hadden: het mooiste kerstcadeau.”
Lees ook: Iconisch geel en groen, de man achter Senna’s beroemde helm: ‘Ayrton wilde opvallen’
Teca25 en Schuberth krijgen groen licht als het papierwerk voor de homologatie een week voor de wintertest is goedgekeurd. “En vergis je niet: daar kan nog heel veel fout gaan. Een verkeerde tekening kan het al verknallen.” In het homologatierapport staat elk onderdeeltje van de helm beschreven. Alle exemplaren die in productie gaan, moeten volgens dit rapport gemaakt worden. “Het telt 67 bladzijden. Alles staat erin, tot elk rubbertje aan toe. Ik heb nog nooit in mijn leven zo veel moeten studeren.”
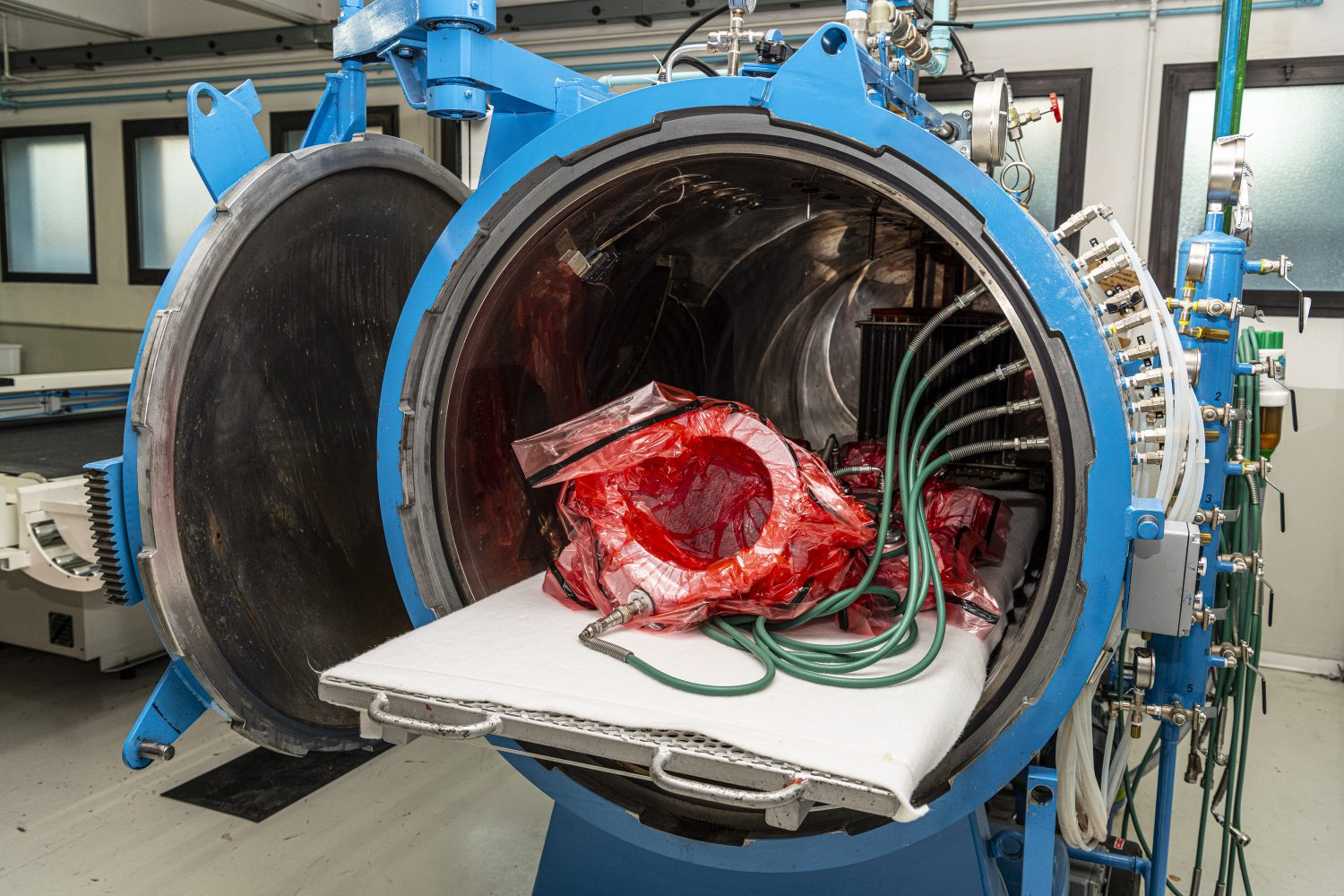
Foto: Schuberth
De productie
Nu de samenstelling van de helm op papier is vastgelegd, kan de Schuberth SF3 in productie. En dat is monnikenwerk, vrijwel alles gebeurt met de hand. “Eigenlijk zijn we een soort luxe horlogemerk.” Het laboratorium van Teca25 is een streng beveiligd gebouw op een afgelegen industrieterrein in Bassana del Grappa. Dall’Oglio herhaalt dat zijn functie als reisleider even wennen is. “Het is de eerste keer dat we deze deuren openen voor mensen buiten het bedrijf. Dit gedeelte proberen we zo veel mogelijk geheim te houden. Er zijn maar een paar bedrijven in de wereld die dit soort producten maken.”
Het team staat onder leiding van Francesco, een vriendelijke zestiger. “Een gek”, noemt zijn baas hem liefkozend. “Maar dat moet ook als je met carbon (koolstofvezel, red.) werkt, anders gaat het niet. Hij heeft al 40 jaar ervaring met composieten, had op tal van andere plekken kunnen werken, maar zijn passie voor racen houdt hem bij ons. We zijn een bedrijf met veel jonge mensen in dienst en zij leren de kneepjes van het vak van hem. Er is heel weinig documentatie over de productie van helmen volgens onze methode. Je kunt composieten studeren, maar het blijft
trial and error. Alles draait om ervaring.”
Lees ook: Verstappen niet van plan om helmdesign elke race aan te passen: ‘Geen tijd voor’
Zoals gezegd: de onderdelen van de helm zijn nauwkeurig vastgelegd en daar mag je in geen geval van afwijken. “Daar zit de moeilijkheid: de mate van herhaling. Je werkt als het ware met je hoofd in een zwart gat waar je constant in kijkt als je urenlang aan het lamineren bent. Aan het eind van de dag kun je duizelig worden, dronken bijna. Met een product als een racehelm zijn foutjes uit den boze. Slecht lamineren, een onderdeel verkeerd aanbrengen, iets vergeten: alles is een veiligheidsrisico.”
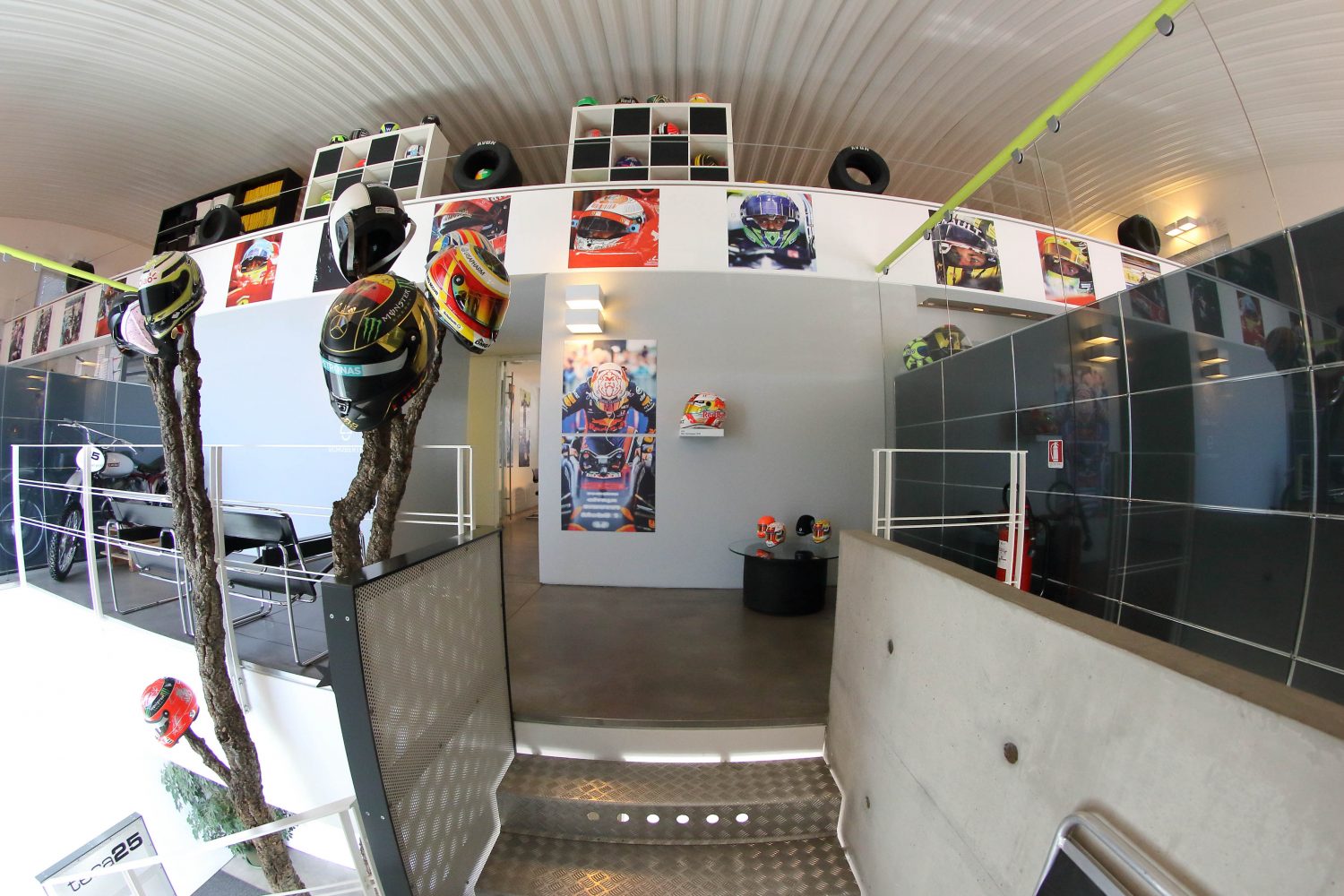
De nauwkeurigheid begint al met de behandeling van de materialen zelf. 70 procent van de helm bestaat uit T1000, een van de schaarste en sterkste materialen ter wereld. Carbon wordt in deze pure vorm eigenlijk alleen voor Formule 1-monocoques en in de ruimtevaart gebruikt. “Het kost zo’n 150 euro per vierkante meter. Om het optimaal te gebruiken moet je het bij 18 graden onder nul bewaren. De rollen worden met koeltrucks aangeleverd en meteen in vriezers opgeslagen. Dat moet binnen een paar minuten gebeuren”, vertelt Dall’Oglio, die een boze blik krijgt van een medewerker als hij de vriezers laat zien en de temperatuur meteen oploopt. “Als je te lang wacht begint het materiaal te werken. En als ik het vast zou houden, gaat het rijzen en wordt het kleverig. Dan krijg ik het niet meer van mijn hand af.”
Lees ook: Coureurs mogen in 2020 weer onbeperkt van helmdesign wisselen
Een machine snijdt de stukjes koolstofvezel op maat, uit een plaat van 2,5 vierkante meter. Het is een wirwar van vormpjes, alles om zo min mogelijk van het kostbare materiaal weg te gooien. Eenmaal gesneden worden de ongeveer 90 onderdelen onder verplicht toezicht van vier ogen gewogen; een gram afwijking is funest. Vervolgens gaan Francesco en zijn team ermee aan de slag. Met een föhn brengen ze vorm in het carbon. “We gebruiken voor een helm een mal, ook van carbon. Daar leggen we de strookjes in, alles nauwkeurig volgens het recept. Een foutje kan gebeuren, maar vijf foutjes kunnen een afwijking van 5 millimeter betekenen. En dan heb je een veiligheidsrisico.”
Op sommige plekken, zoals de strook boven het vizier die het voorhoofd beschermt, zitten liefst achttien lagen T1000. Voor andere gedeeltes van de helm, die de directe impact van een crash moeten absorberen, wordt een ander soort carbon gebruikt dat flexibeler moet zijn. Dit proces heet lamineren en duurt vier uur. Daarna gaat de mal inclusief legpuzzel van vijf soorten koolstofvezel in de oven.
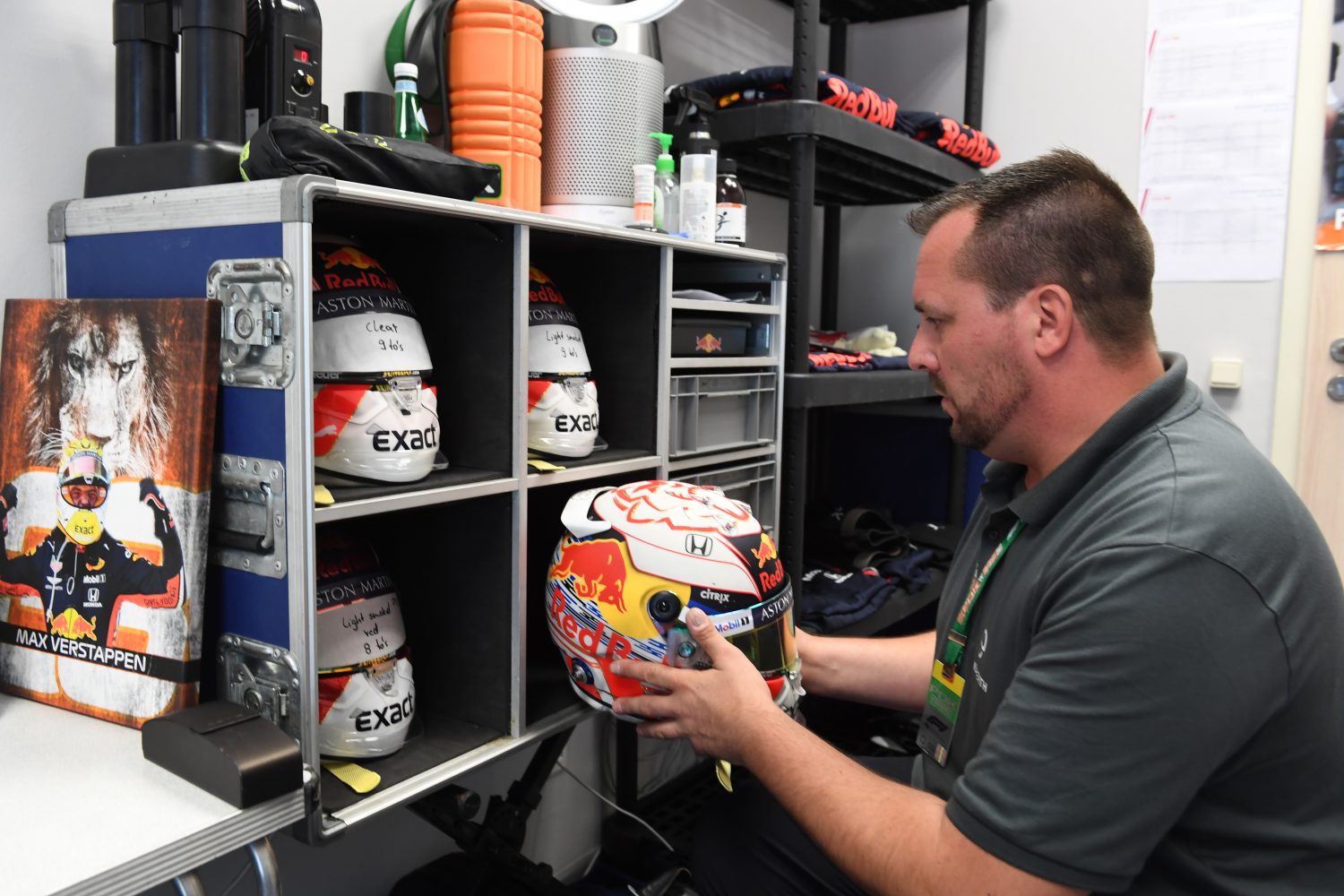
Sven Krieter Foto: Motorsport Images
De klanten
Als de schelp is gespoten, bijvoorbeeld door Verstappens helmontwerper Jens Munser, gaat technicus Sven Krieter van Schuberth in het Oost-Duitse Maagdenburg aan de slag met de binnenkant. Iedere coureur heeft een andere maat hoofd, met andere vormen. “Carlos Sainz heeft van onze klanten het grootste, dat van Verstappen is iets kleiner. Michael Schumacher had een heel klein hoofd”, vertelt Krieter, sinds 2004 het gezicht van Schuberth in de paddock.
Lees ook: Manager Vermeulen verbaast Red Bull nog altijd met acties rond Max Verstappen
Hij bezoekt elke race, bijna 300 inmiddels, en neemt de helmen mee om ze persoonlijk af te leveren bij de coureurs. Bij elk team heeft hij een hokje waar hij de helmen prepareert. “Dat vergt een enorm vertrouwen, want ik zie alle geheimen, maar gelukkig weet ik niets van techniek, haha. Ik houd de weersvoorspelling in de gaten en weet van iedere coureur voor elke situatie welk vizier hij gebruikt.” De coureurs hebben een eigen dossier met maten tot achter de komma, een extra kussentje hier, minder padding daar. En zo zit de helm na een lange weg gegoten als een maatpak.
Dit is de helmtest
- Frontale en zijdelingse impact waarbij het hoofd van de coureur niet mag blootstaan aan meer dan 275 G bij hoge snelheid en 200 G bij lagere snelheid.
- De ‘Massa-test’: een projectiel van 225 gram wordt met een snelheid van 250 kilometer per uur afgevoerd op verschillende plekken van de helm.
- Een gewicht van 10 kilo wordt van 5 meter hoogte op de bovenkant en de zijkant van de helm losgelaten.
- Een gewicht van 4 kilo valt op de helm met een snelheid van 30 kilometer per uur.
- Kogeltjes van 1,2 gram worden op het vizier afgevuurd met een luchtdrukgeweer.
- Trekken aan de sluiting om vast stellen dat de helm nooit zal losschieten.
- Ook het gedeelte onder het vizier krijgt klappen met een hamer en moet die absorberen zonder dat de energie te veel op het hoofd inbeukt.
- De helm moet bestand zijn tegen temperaturen tot 800 graden en bij brand moeten de vlammen vanzelf doven.